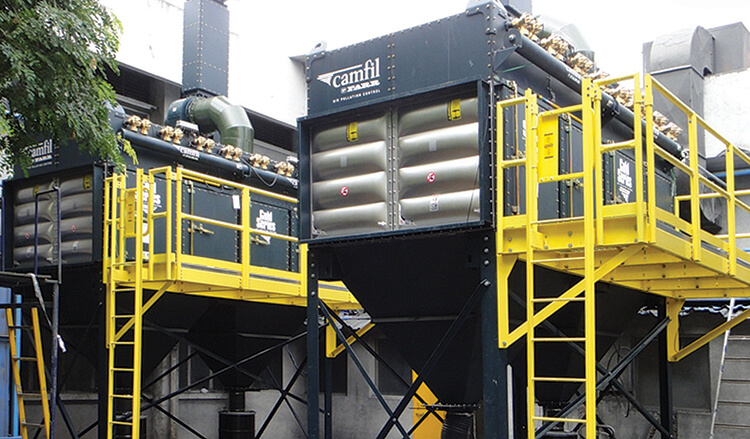
Challenge
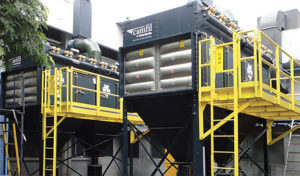
Two Gold Series GS 32s replace Torit dust collectors at Vishay Components.
Vishay is one of the largest manufacturers of semiconductors and passive components in the world. They have several plants spread across the Americas, Europe and in Asia, including India. In India, Vishay Components uses thermal spray booths with Torit dust collectors imported from Europe as a part of the manufacturing process.
Vishay used two Torit models — 3DF 36 C-R dust collectors — for spraying zinc and aluminum in their two metal spray booths, and a local unknown dust collector for their epoxy coating application. Vishay was concerned with two main issues: dust spreading in their thermal spray and epoxy coating booths and higher emission levels, which the old dust collectors were not able to handle to Vishay’s satisfaction. In January 2012, they approached Camfil India for a possible solution.
Solution
Camfil India and Camfil APC Malaysia worked with India as the sales and marketing front and Malaysia as the technical front. In October 2012, after a series of surveys and presentations, Vishay placed an order for two GS32s (for the metal spray booths) and one GS6 Gold Series® industrial dust collector (for the epoxy coating machines) complete with explosion vents and mechanical isolator dampers. They reached the customer in January 2013 from the Jonesboro plant. In addition to the new Camfil dust collectors, the entire ductwork was replaced and designed by Camfil. The dust collectors were installed and commissioned in June 2013 under Camfil APC Malaysia’s supervision.
Notable improvements documented by Vishay include:
- Decreased (nearly eliminated) spread of dust in booths due to suction velocities being nearly doubled, resulting in cleaner booths and rooms and happier employees.
- Lowered energy costs due to replacing Torit collectors using 20 HP motors with energy efficient collectors using 10 HP motors.
- Significantly lower operational costs for the dust collector when compared to the Torit system.