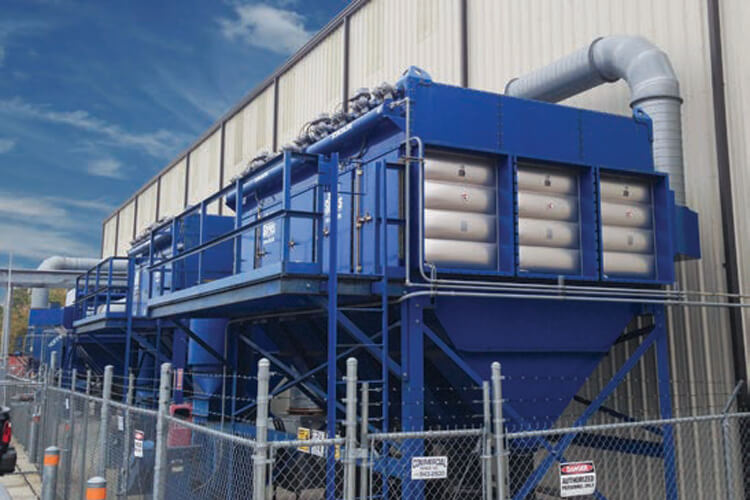
Challenge
Sulzer is a leading independent service provider for all brands of rotating equipment, such as turbines, pumps, compressors, generators, and motors. At their Texas location, explains Joe Drury, division superintendent at Sulzer, “Rotating equipment is removed from the site, dissembled, inspected, repaired, coated, assembled, and installed at the customer site. The repair and coating processes can require dust collection.”
Sulzer knew that compliance with environmental, health, and safety regulations was not only important, but also necessary. In 2005, they began installing Gold Series units as the location expanded. Sulzer replaced several aging dust collectors with Gold Series units due to performance gains and reduced maintenance. Drury mentioned, “Other unit designs led to leaks at filter seals during service.”
Solution
From 2005 to 2009, Sulzer installed a total of 15 Gold Series® industrial dust collector units of varying models — from GS6 up to GS60. The units have proven themselves by improving Sulzer's work environment. They installed the GS36, GS48, and GS60 on their thermal spray applications and the 12 GS6 units on their metal grinding applications.
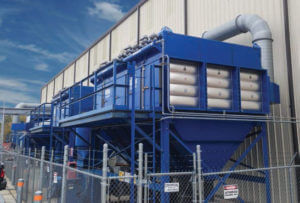
A GS36, GS48, and GS60 on thermal spray.
“We installed the Gold Series collectors in the coating shop, where we do grit blasting, HVOF, and air plasma coatings, and in our component repair shop, where we do welding, blending, and grinding on gas turbine components,” Drury said. “The main improvements we've seen are increased filter life, increased suction, and decreased collector maintenance."
Drury cited the modular design and construction of the Gold Series units as its best features. “Maintenance is moderate to none. Removing and cleaning filters is much easier than competitor units,” he continued. The units have alleviated the problems Sulzer faced — no more leaks, easier maintenance, and longer filter life.