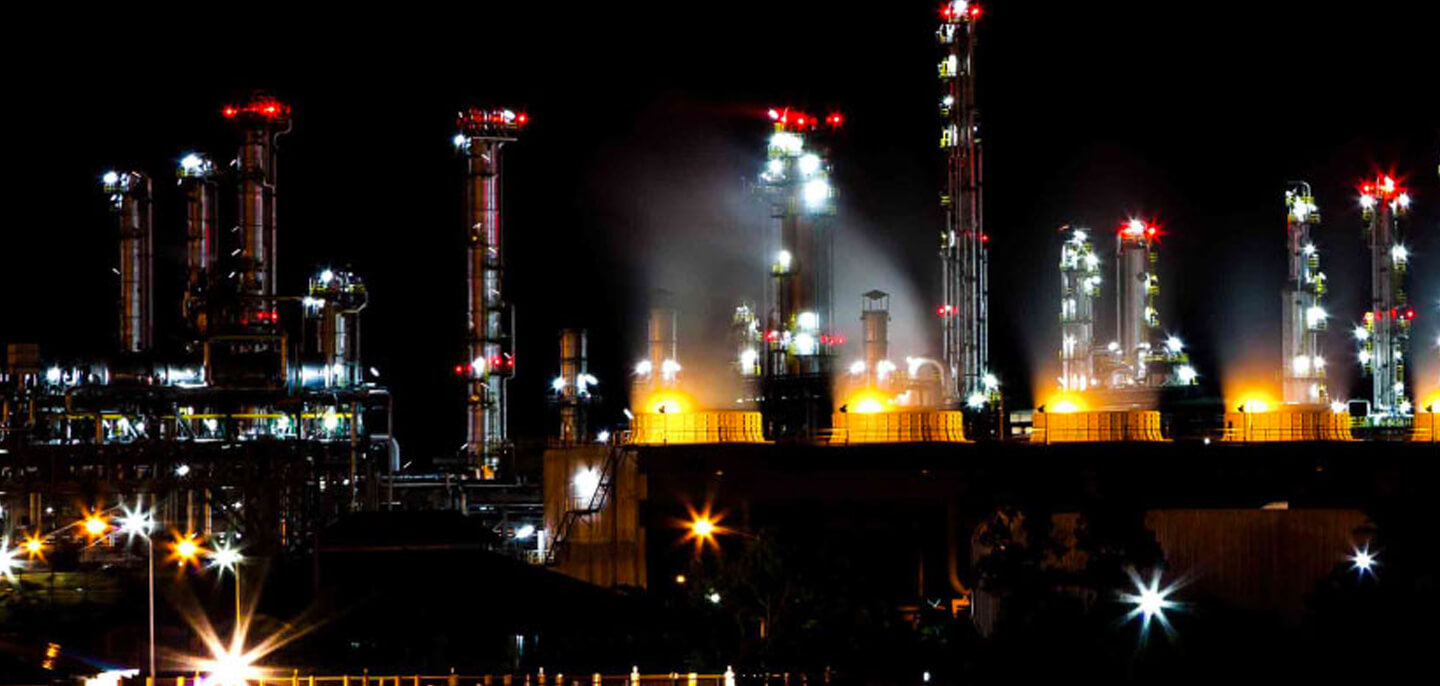
CHEMICAL DUST HAZARDS
Chemical manufacturers create the adhesives, foams, plastics and other raw materials that are used to make most consumable products. Many use batch mixing and other processes that create dangerous dusts. When operators handle these materials or convey or dump them into processing equipment, the dust becomes airborne and endangers air quality.
Airborne chemical dusts can be hazardous to workers, equipment, manufacturing plants, and the environment. They can be toxic as well as combustible. In addition, airborne dusts can cross-contaminate products, putting the end users of those products at risk and exposing manufacturers to liabilities.
Industrial Dust Collectors Contain Dangerous Chemical Dusts
OSHA recommends that facilities maintain workplace air quality through “engineering and work practice controls” where feasible. Dust collection systems are the most cost-effective way to improve air quality in a chemical manufacturing or processing facility. They work around the clock, using advanced filtration technology to safely capture and contain airborne dust and contaminants.
Camfil APC’s premium-quality dust collectors cost-effectively collect many types of chemical dust, including toxic dusts, combustible dusts, cross contaminant dusts, and nuisance dust. They ensure that all employees can work safely in facilities where toxic chemical dusts are present. They:
- Save time, money and energy on dust collection
- Protect people, property and environment from dust hazards
- Prevent cross contamination
- Satisfy compliance with OSHA, NFPA and EPA
Chemical dusts are dangerous in the workplace when they have high concentrations of elements like crystalline silica that are toxic in the body at certain concentrations.
Some dusts simply react badly with skin and eyes. Other chemical dusts are fine particles that can travel deep into the body, damaging the kidneys, lungs, brain, intestines, and prostate.
For these reasons, OSHA now regulates toxic dusts and failure to comply can lead to serious fines and other legal problems. For example:
- Worker exposure to mineral elements like silica dust causes respiratory problems, from chronic bronchitis to lung cancer.
- Worker exposure to metallic elements, such as cadmium, beryllium, arsenic, chromium, and lead, causes neurological, gastrointestinal and reproductive damage.
OSHA has established permissible exposure limits (PELs) for chemical substances that endanger workers. Here are some examples of the PELs for various chemical dusts:
- Cadmium: 5 µg/m3
- Zinc oxide: 15 mg/m3
- Chromium: 5 µg/m3
- Iron oxide: 15 mg/m3
- Cobalt: 1 mg/m3
All Camfil APC dust collectors safely contain toxic dusts.
Many chemical dusts also qualify as combustible dusts, including ascorbic acid, calcium acetate, dextrin, lactose and sodium ascorbate. These chemical dusts can accumulate on surfaces, where any spark or flame can ignite them, causing a fire or explosion. Common ignition sources are kilns or welding flame, but it can even be a lit match or cigarette.
Combustible dust explosions threaten workers and capital assets like buildings and equipment. A powerful dust explosion can injure or even kill plant workers and destroy buildings and equipment.
Dust collectors minimize the amount of combustible dust that can collect on floors and other surfaces, and they contain chemical dust in one area. But the dust collectors themselves can be a fire or explosion hazard if they are designed incorrectly or not equipped with controls that prevent deflagration and contain explosions. These controls include fire retardant cartridges, sprinkler connections, explosion vents, suppression systems, and backdraft dampers.
All Camfil APC dust collectors safely contain combustible dusts and are equipped with deflagration controls.
Airborne dust can also be a major housekeeping problem because it eventually settles on floors and surfaces. A dirty-looking facility can hurt your brand and make a negative impression on customers, potential employees, and other visitors. Not only is the dust a nuisance to keep off floors and overhangs, but it can accumulate on equipment and electronics, causing them to malfunction or fail.
All Camfil APC dust collectors safely contain nuisance dusts.
- What type of cartridge and filter media is best?
- Is an intermittent-duty, continuous-duty or variable frequency collector best?
- Are explosion protection controls required?
- Which style and size configuration are best?
- Will the dust collector use compressed air?
The true cost of a dust collector goes far beyond your investment in capital equipment of the system components themselves and ductwork. We help you select the best dust collector systems for your application, with the lowest energy and operating expenses.
This means calculating the total cost of your dust collection system, taking into consideration the costs for energy, replacement filters and downtime for maintenance. We have a rig dedicated to ANSI/ASHRAE Standard 199 testing to give you real world, apples-to-apples comparison data on our dust collectors. Data like emissions, pressure drop, compressed air usage, energy consumption, and emission readings shows you the real costs to operate the collector over time and make accurate system comparisons.
Resources and Literature:
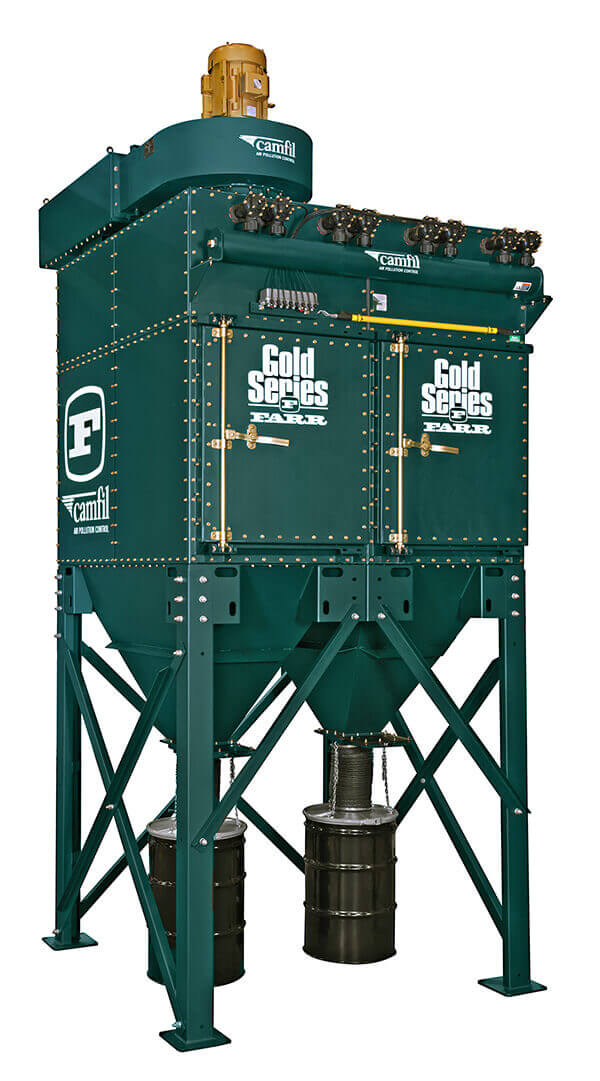
FARR GOLD SERIES INDUSTRIAL DUST COLLECTOR
The Farr Gold Series The Farr Gold Series dust collector performs well in applications where dry materials are batch mixed, conveyed and processes. The Farr Gold Series offers high performance, a modular design, ease of service, and an optional bag-in, bag-out filter change out. Constructed from heavy-duty carbon steel to meet the demands of your application, the Farr Gold Series has unparalleled strength and life compared to the competition. Coupled with Gold Cone™ vertical cartridge technology, the Farr Gold Series offers superior pulsing of high-loading dust while simultaneously utilizing the smallest floor space of any dust collector available today.
- High-efficiency filters capture 99.99% at 0.5µ of the dust.
- Gold Cone™ vertical cartridge technology that provides 25% more media for long service life.
- Timer control module for automatic pulse filter cleaning based on differential pressure readings.
- Quick-open heavy gauge doors for fast access to the filter cartridge change-out system.
- High entry cross flow inlet eliminates upward can velocities that hold fine powder in filters, reducing re-entrainment of the fine particles.
- Abrasion resistant inlet configuration knocks most dust into the hopper before it gets to the cartridges.
- Specially treated filter media repels fine particles, for lower pressure drop and long filter life.