How to Evaluate Dust Collection Costs
Running a dust collector efficiently can save a lot of money
June 14, 2021
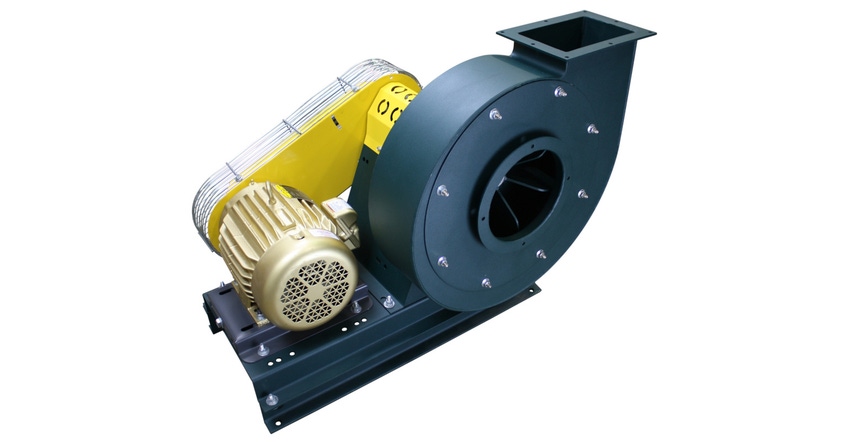
Taylor Morgan, regional manager, Camfil Air Pollution Control
Capturing, conveying, and containing dust is a serious challenge for facilities across many different industries that handle dry processing and bulk solids. A cartridge-style dust collection system designed and installed specifically for your operation works to prevent personnel from developing respiratory problems, avoid products from being cross contaminated, and keep facilities in compliance with air quality and employee health requirements.
Whether you are considering purchasing a new dust collection system, looking for cost-effective ways to operate your current collector, or selecting the best replacement filters to purchase, every dollar counts. Here are important considerations for evaluating dust collection costs.
Understand Costs Involved with Dust Collection
When evaluating the costs of operating cartridge-style dust collectors, many companies base buying decisions solely on the equipment’s purchase price. However, since dust collectors last 20-30 years, operating costs become much more significant over time, such as energy usage and consumables. Evaluating the total cost of ownership, including electricity, compressed air usage, and ongoing expenses associated with filter cartridges, will provide a more accurate and meaningful cost comparison.
Dust collectors consume electrical energy the entire time they are running, but the largest portion of the electrical load goes to the fan motor that moves the air through the system. In addition, if the dust collection system is not designed to recirculate the air that it constantly extracts back to the plant, a lot of energy is used to heat or cool the air that replaces it.
Manually Adjust Airflow to Save Energy
Dust collector fan motors typically have a damper at the outlet that can be used to manually alter the airflow and static pressure. When the filters are new, you can close the damper more to achieve the desired airflow. As the filters become dirty, you can open the damper more to increase airflow. However, this is time-consuming and requires operator diligence.
Reduce Costs with Variable Frequency Drives
A variable frequency drive (VFD) is an electrical device that controls the fan speed. It automatically manipulates the frequency and power consumption supplied to the fan motor, so human interaction is not required. The VFD automatically senses changes in airflow and pressure drop and adjusts the fan speed to return the system to optimal airflow.
Dust collector variable frequency drive to control fan speed.
VFDs achieve significant electrical savings over the long term because the amount of energy needed to operate the fan motor varies with speed. With a VFD, the fan draws only the amount of power required for the specific fan speed.
For example, a fan that runs 25% slower would use 42% of the power that would be required for full speed. The same fan running 50% slower would use 12% of the full speed power. VFDs enable users to save an average of 30% on their energy costs to operate the dust collector. Also, maintenance and operation costs are reduced because fan speed adjustments do not require human intervention.
VFDs generally cost $11,000 to purchase and install. However, since they often save more than $12,000 per year in energy, they can pay for themselves in under a year.
Decrease Compressed Air Consumption
Most modern dust collectors require pulse cleaning to maintain a steady airflow (cu ft/min) and run at peak efficiency. As filters fill up with dust, airflow becomes restricted, which increases the system’s differential pressure (pressure drop). When the pressure increases to a pre-determined level, pulse-cleaning systems send quick bursts of compressed air back through the filters to dislodge the dust from the filters so it can drop into a waste bin. However, producing compressed air is expensive, so it is worthwhile to get a dust collector that minimizes usage. Today’s most advanced dust collectors can reduce compressed air consumption by as much as 50% versus competitive dust collectors. They use less compressed air because they are able to pulse-clean far less often.
Maintain Airflow While Using Less Compressed Air
When properly designed, a dust collector’s cleaning system will remove the accumulated material from the filter cartridges, reduce the pressure drop across them, and lower the fan energy consumption. Together, these factors reduce associated energy costs. High-efficiency filter cartridges can handle higher airflows while maintaining a high level of filtration efficiency. Pleated filter media enables each filter cartridge to contain more usable media so they can move more air and process more dust.
Cartridges fabricated with inner cones of additional pleated filter media also improve operating efficiency because they can evenly distribute the pulsed air along the outer pack of the filter and through the inner cone. With each pulse, more dust is ejected from the filters straight into the hopper. The result is a more thorough cleaning with each pulse, so the airflow remains unrestricted, and the pressure drop remains low for a longer period of time.
Minimize Heating and Air Conditioning Costs
Dust collection systems move a great deal of air from the facility they are cleaning. Dust collectors generally draw in the dust-laden air, send it through the filters to extract the dust, and then expel it outside via ducting. When the inside air is heated or air conditioned, the facility’s HVAC system has to work hard to continually replace the air that was removed.
Plants can reduce their energy usage by recirculating the cleaned air back into the workspace. However, if the facility produces combustible dust, air cannot be safely recirculated without a filter on the return ducting that prevents the dust from re-entering the workspace if there is a leak in the primary filter system. A properly tested and documented integrated safety monitoring filter (iSMF) provides that function without using additional floor space. The iSMF also serves as a flame arrestor for combustible dust, making it safe for facilities handling combustible dust to recirculate their air.
Integrated safety monitoring filters atop an industrial dust collector system.
Lower the Cost of Replacing Filters
Filter cartridges are a major cost consideration because they have to be continually replaced over the life of your collector. Filter purchase price is not the main cost consideration since higher priced filters generally last much longer than cheaper replacement filters because they pulse-clean more effectively. Be sure to get a dust collector that is designed for your specific dust and application, so it provides the required airflow with the minimum number of cartridges. Premium filter cartridges generally last 50% longer than standard filters, but you would likely need less of them during the year, reducing your overall filter cost. Because they are changed out less frequently, they have lower associated maintenance, transportation, downtime, and disposal costs. Disposal costs can be significant, particularly if you are collecting a hazardous material and the filters require incineration.
Most premium filter cartridge brands can be constructed with standard media or specialty media for specific types of dust and/or specific applications. For example, certain applications may require media treated with coatings that promote dust release, flame retardance, or conductivity. Using the wrong media can cause unsafe operating conditions, a combustible dust hazard, high pressure drop, and excessive energy use. Using the correct media creates a safer, cleaner work environment with less dust collector maintenance.
Examples of various types of media for industrial dust collector filter cartridges.
Use a Filter Monitoring System
When a dust collector vendor monitors its customers’ dust collectors remotely via sensors on the filtration system, they get alerts when differential pressure increases. This generally means the filters need to be replaced or there is another issue they have not noticed. For example, someone might have forgotten to turn on the cleaning system or the compressed air, so the filters have not been cleaning. These monitoring systems are good preventive maintenance tools that reduce the overall downtime costs.
Networking and sensor device that remotely monitors operation of an industrial dust collector.
Final Thoughts
Running a dust collector efficiently can save a lot of money on energy costs and consumables. To find the best value, fully analyze all costs involved in operating your dust collection system.
Taylor Morgan is a regional manager for Camfil Air Pollution Control (APC), where he has worked since 2012. He is responsible for territory development, product implementation, and problem-solving industrial ventilation applications within TX, NM, OK, and LA. For information, call 800-479-6801, email [email protected], or visit www.camfilapc.com.
You May Also Like