Maximize Safety When Working With Combustible Dust
By: Andy Thomason, Contributor
All it takes for a dust explosion to occur at your facility is for oxygen, an ignition source, and a combustible dust cloud to come together in a confined space. If your operation generates dust, you probably already have some mitigation processes in place. However, to ensure that your efforts are effective enough, it is important to understand the nature of a dust explosion; what to include in your safety plan; regulatory requirements; and how to safely maintain your dust collection system.
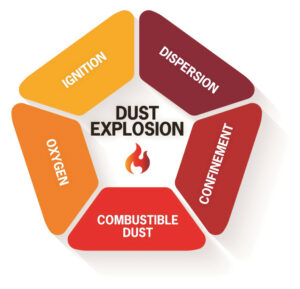
After an initial explosion or deflagration event, elastic rebound shockwaves occur, which cause more dust clouds. Secondary deflagrations and explosions are caused by the dust clouds jarred loose from the primary explosion. The explosion pentagon repeats itself until one of the five elements is no longer present. (Image courtesy Camfil APC)
Explosion Event
After the initial explosion or deflagration event, elastic rebound shockwaves occur, which cause more dust clouds. Secondary deflagrations and explosions are caused by these dust clouds jarred loose from the primary explosion. The explosion pentagon repeats itself until one of the five elements is no longer present. All this happens in an average time span of less than 500 milliseconds.
Combustible Dust Safety Planning
Some accidents are unpreventable, but the consequences can be limited. Many accidents can be avoided with the proper education, planning and equipment.
Training: A vital component to a combustible dust safety program is educating personnel to recognize unsafe conditions. Training ideally should include what conditions to watch out for; how to report them to management; when it is necessary to take preventative action; and what steps to take to mitigate possible disaster. This means, in addition to OSHA-required training in work safety applicable to their specific jobs, workers should learn about facility programs for controlling ignition sources and dust. This includes pre-employment training and ongoing education, especially if their duties or processes change. Managers and supervisors also need to know how to process information received from workers, so unsafe practices can be addressed immediately.
Key Safety Program Components: Although the specifics of a combustible dust safety program depend on the processes taking place, it should include the following core elements:
-
This image shows dust accumulation at an industrial facility. (Image courtesy Camfil APC)
Facility analysis to identify open and hidden areas where combustible dusts might accumulate; ways in which the dust could be dispersed into the air; and potential ignition sources
- Process hazard analysis, which OSHA requires on each process point generating dust
- Dust hazard analysis, which the National Fire Protection Association (NFPA) requires, to determine if the process-generated dust is explosive
- Plan detailing how to remove the dust hazard from each process
- Housekeeping policy describing cleaning processes to control the buildup of combustible dust
- Maintenance and inspection schedule to keep equipment operating properly and in compliance with relevant regulations
- Detailed plan on how to execute, manage and adjust the elements of the combustible dust program
NFPA Standards
The NFPA sets safety standards for managing combustible dust. NFPA standards are not laws, but you should take them very seriously, because failure to comply puts your facility and workers at risk for devastating combustible dust fires and explosions. In addition, OSHA uses these standards to evaluate risk and cite safety violations. Noncompliance can also lead other authorities having jurisdiction (AHJ) to withhold permits or insurance companies to deny coverage.
These are the main NFPA standards you need to know if your facility handles combustible dust:
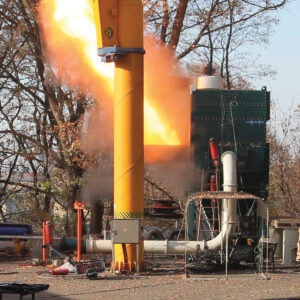
The NFPA sets safety standards for managing combustible dust. While they are not laws, they should be taken seriously; failure to comply puts the facility and workers at risk for devastating combustible dust fires and explosions. (Image courtesy Camfil APC)
NFPA 652 Combustible Dust Standard provides requirements for managing combustible dust fires and explosions across industries, processes and dust types. As noted above, owners or operators of a facility that generates combustible dust must conduct a dust hazard analysis; develop a plan for managing fire and explosion dangers; and provide training for workers who potentially could be affected by the hazards. A dust hazard analysis includes the process machinery that produces dust and the dust collection system itself.
NFPA 654 Standard for Preventing Fire and Dust Explosions from Combustible Particulates applies to all phases of the manufacturing, processing, blending, conveying, repackaging and handling of combustible particulate solids or hybrid mixtures, regardless of concentration or particle size. It defines requirements of facilities for process hazard analysis, management of process change, performance-based design requirements, facility and system design, and process equipment explosion protection.
The performance-based design option specifies that, if the AHJ approves of another method for protecting your dust collector from explosions, you can use that method instead of one specified in the standard. An example of an AHJ is a local or regional public safety authority, such as a fire marshal.
NFPA 68 Standard on Explosion Protection by Deflagration Venting covers all prescriptive and performance-based design requirements and calculations for deflagration venting. These systems vent combustion gases and pressures resulting from a deflagration within an enclosure in order to minimize structural, mechanical and physical damage.
NFPA 69 Standard on Explosion Prevention Systems prescribes the design of prevention controls including inlet and outlet ducting, spark-extinguishing systems and methods for preventing an explosion from traveling back into the building or to process locations upstream of inlet ductwork.
NFPA 484 Standard for Combustible Metals magnifies the level of attention needed for applications dealing with metal dust types because of the severity of explosions and ease of ignition of metal dust. It also applies to processing or finishing operations that produce combustible metal powder or dust.
NFPA 61 Standard for the Prevention of Fires and Dust Explosions in Agricultural and Food Processing Facilities covers requirements for operations that handle, process or store dry agricultural bulk materials, including grains, oilseeds, agricultural seeds, legumes, sugar, flour, spices, feeds, starch and other related materials.
Safe Operation of the Dust Collection System
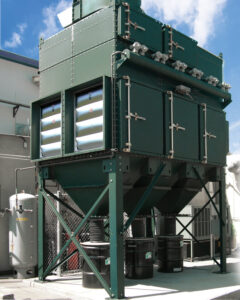
Dust collection systems should include protection equipment, such as explosion venting. A dust explosion in an unprotected dust collector produces a high-pressure wave that can fragment the housing and send heat, flames and dangerous projectiles into the surrounding area. (Image courtesy Camfil APC)
Using a dust collection system that is properly designed for your specific operation can significantly reduce combustible dust in the work environment. However, the dust collection system itself can be a source of an explosion—if it is not protected. This is because dust collectors are closed vessels full of dry particles that can form a dust cloud and become ignited if the fan draws in a spark or flame from outside of the collector. Therefore, it is imperative to outfit the dust collection system with protection equipment, such as explosion venting. A dust explosion in an unprotected dust collector produces a high-pressure wave that can fragment the housing and send heat, flames and dangerous projectiles into the surrounding area.
If your facility produces or processes combustible dusts, your collection system must be equipped with deflagration protection as set by the applicable NFPA Standards. You can add prescriptive controls to protect the system or performance-based controls. Camfil’s integrated safety monitoring filter is an example of a performance-based control device.
An integrated safety monitoring filter (also called an iSMF) installed on the top of a dust collector protects the downstream equipment and work area, because it acts as a flame front barrier. Flameless vents can be installed over a standard explosion vent to extinguish the flame front as it exits the vented area, stopping it from leaving the device.
Mitigating Risk
Dealing with combustible dust is a challenging but necessary duty. Fortunately, combustible dust is a hazard that can be managed, to a great extent, with thorough planning and attention to detail. Understanding the recipe for an explosion; developing a safety program; and incorporating the appropriate NFPA-compliant explosion protection devices on your dust collector can help you manage the risk of personnel injury and damage to your equipment and facility.
About the Author
Andy Thomason is the Senior Applications Specialist at Camfil Air Pollution Control (APC), where he provides application support to the sales and customer base and technical support to new product development. For information, contact 800-479-6801 or 870-933-8048; email filterman@camfil.com; or visit www.camfilapc.com.
Share on Socials!
Age “Correction” in Hearing Conservation Programs
Computer Use Guide
Location Tracking: Integral to Lone Workers’ Safety
Leaders in Industrial Hygiene
Council for Accreditation in Occupational Hearing Conservation (CAOHC)
Subscribe!
Sign up to receive our industry publications for FREE!